The challenge
Conventional temperature sensors, such as thermocouples or resistance thermometers, are widely used to monitor and control a huge range of processes from manufacturing aircraft engine turbine blades to sterilising food products.
However, they don’t measure the temperature directly, instead they typically possess some property, such as voltage or resistance, which varies with temperature and can be measured. These thermocouples or resistance thermometers therefore need calibrating regularly, so that users can have confidence in the measurements. This can be costly and time-consuming.
For some industrial applications, especially where the temperature measurement is linked directly to user safety, such as in aviation, or where there is also gamma radiation present, any improvement in confidence that can be made is crucial to support innovation.
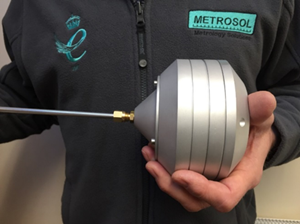
To overcome the need for calibration, the thermometer must measure temperature directly.
This has not been done before, at least, not for practical in-contact measurements without large rooms of highly expensive electronic equipment!
The thermometer must not be sensitive to any degradation of the component materials and, ideally, be able to be used in environments with high temperatures, contamination, vibration and ionising radiation.
Eliminating the need to keep checking the performance of the thermometer would improve production efficiency, as periodic removal and replacement would not be needed, saving both time and money.
The solution
NPL has been working with Metrosol Limited, an SME specialising in the development of sensing electronics, to build a proof-of-concept Johnson noise thermometer. By measuring the tiny electrical fluctuations associated with the random thermal motion of charge carriers (the Johnson noise), the temperature can be determined directly, even if the sensor material degrades during exposure in harsh environments, such as high temperatures or ionising radiation. Effectively, all properties which affect the temperature measurement can be measured continuously, so the thermometer always yields the correct temperature.
Johnson noise thermometry is well established in the laboratory and it is used in primary thermometry and Boltzmann constant determinations, but it has not been used for practical devices in industrial environments. Whilst there have been many attempts to develop a practical device, various shortcomings of the electronics or sensor design means that a practical noise thermometer is still not commercially available.
For the first time, a robust, industrially-oriented device has been developed, drawing on new technology that can ultimately be commercialised. Metrosol, with key support from NPL, has developed a working practical Johnson noise thermometer, which has achieved its target accuracy of better than 1 °C.
The impact
This technology offers huge advantages over conventional practical sensors, such as thermocouples or resistance thermometers, which exhibit calibration drift and progressive loss of accuracy in harsh environments.
Because the practical Johnson noise thermometer is independent of any calibration and it can measure all parameters which are needed to yield the true temperature, it represents a breakthrough in temperature sensing, particularly in harsh environments. The device can be used with confidence for prolonged periods without the need for recalibration and replacement. This results in improved process control and better efficiency, in terms of energy use, product yield and reduced process downtime.